Professional Houston Welding Inspection: Making Sure Architectural Honesty and Safety
Exactly How Welding Assessment Functions: An Extensive Evaluation of Methods, Criteria, and the Role of Assessors in Making Certain Architectural Integrity and Safety
Welding evaluation is a necessary element in the building and construction and production industries, where the honesty of welded joints is vital to safety and security and dependability. Assessors are entrusted with not just evaluating weld quality versus rigid requirements yet also interpreting complex codes and criteria.
Significance of Welding Assessment
Welding inspection is vital in guaranteeing the honesty and safety of welded structures, with research studies suggesting that up to 70% of architectural failures can be traced back to inadequate welding practices. This emphasizes the value of methodical evaluation procedures throughout the welding lifecycle, from prep work to completion. Effective evaluation not only determines problems prior to they escalate into substantial problems however additionally guarantees conformity with industry requirements and guidelines.

The function of welding assessors extends beyond simple quality assurance; they are important in protecting public security and lessening liability for companies. By carrying out rigorous examination methods, companies can discover problems such as insufficient combination, fractures, or extreme porosity, which can endanger the overall toughness of a bonded joint. Recurring training and accreditation of examiners contribute to the overall quality assurance in welding operations, cultivating a culture of security and quality.
On top of that, welding examination plays a critical duty in preserving operational effectiveness. Recognizing flaws early while doing so assists in timely restorative actions, reducing costly rework and task delays. Inevitably, a robust evaluation structure works as a foundation for trustworthy and resilient welded frameworks, guaranteeing they meet both practical and safety needs.
Common Evaluation Methods
How can one ensure the top quality of bonded joints throughout the inspection procedure? The implementation of different evaluation approaches is crucial in evaluating weld integrity and determining prospective issues. Common approaches consist of Visual Inspection (VT), which is typically the first line of defense, permitting inspectors to find surface area flaws such as splits, porosity, or incomplete blend by aesthetically evaluating the welds.
Ultrasonic Evaluating (UT) is an additional extensively used method, employing high-frequency sound waves to identify internal flaws within the weld. This technique is specifically efficient for spotting concerns that are not visible to the naked eye. Radiographic Checking (RT) utilizes X-rays or gamma rays to develop photos of the weld, making it possible for the identification of volumetric flaws, such as incorporations or spaces.
Magnetic Bit Evaluating (MT) and Liquid Penetrant Checking (PT) are likewise popular methods, focusing on surface area flaws. MT counts on magnetic areas to disclose surface area and near-surface discontinuities, while PT involves applying a liquid dye to highlight flaws. Each of these methods serves a distinct objective, guaranteeing the detailed analysis of bonded joints and safeguarding structural honesty and safety.
Criteria for Evaluating Welds
The assessment of welds is directed by a set of well established standards that ensure both functionality and safety and security in welded frameworks. These requirements incorporate various factors, including weld size, profile, and penetration, which must adapt specified standards. Conformity with market codes, such as those set by the American Welding Culture (AWS) or the American Culture of Mechanical Designers (ASME), is necessary in identifying the acceptability of a weld.
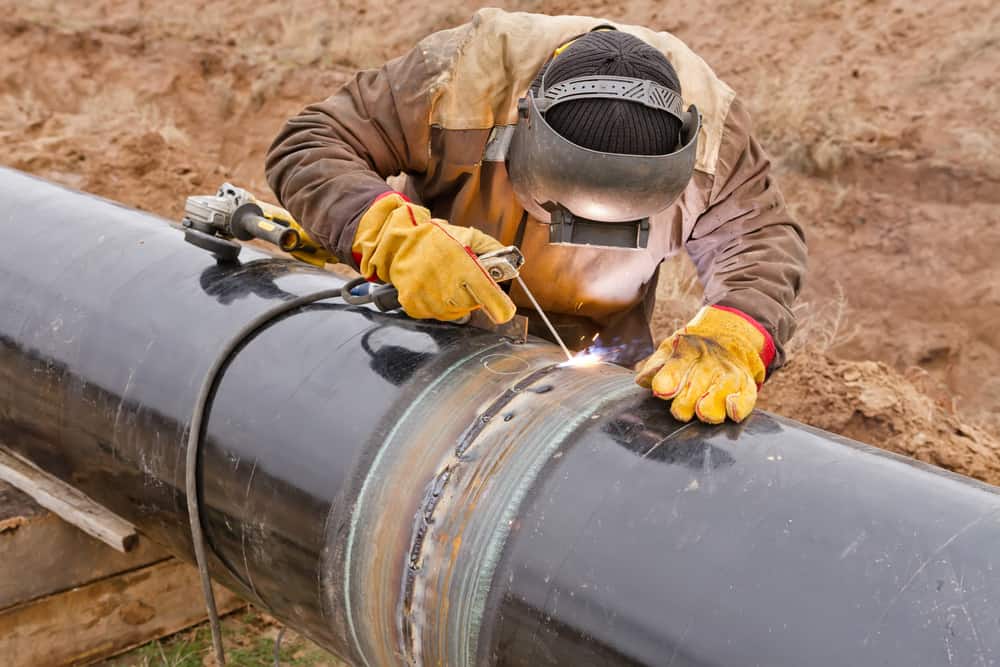
Weld metallurgy plays an important role; the assessment considers the combination high quality between base and filler materials, as well as heat-affected zones. The general mechanical homes, including tensile stamina and ductility, have to satisfy the demands developed for the particular application. Collectively, these requirements make certain that welds not just meet aesthetic requirements but likewise carry out reliably under functional conditions.
Role of Welding Inspectors
A welding inspector's proficiency is essential in making certain the stability and high quality of welded structures. These specialists play a critical role in the fabrication and construction procedure by verifying that welding procedures stick to established standards and specifications. Their duties include an extensive series of jobs, including aesthetic evaluation of welds, examining welding paperwork, and carrying out non-destructive testing (NDT) methods such as radiographic or ultrasonic screening to determine flaws.
Welding inspectors are likewise in charge of interpreting welding codes and standards, guaranteeing that the welders are certified which the products utilized satisfy the necessary requirements - Houston Welding Inspection. They need to maintain careful documents of inspections, which act as documents of conformity and quality control. These assessors typically work together with designers and project supervisors to deal with any issues that emerge during the welding process, providing suggestions for restorative activities when required.
In addition to technical abilities, effective interaction is vital, as welding assessors have to convey findings clearly to stakeholders and facilitate training and guidance for welders. Eventually, their duty is essential to maintaining safety and dependability in welded structures, contributing dramatically to the total success of building and construction tasks.
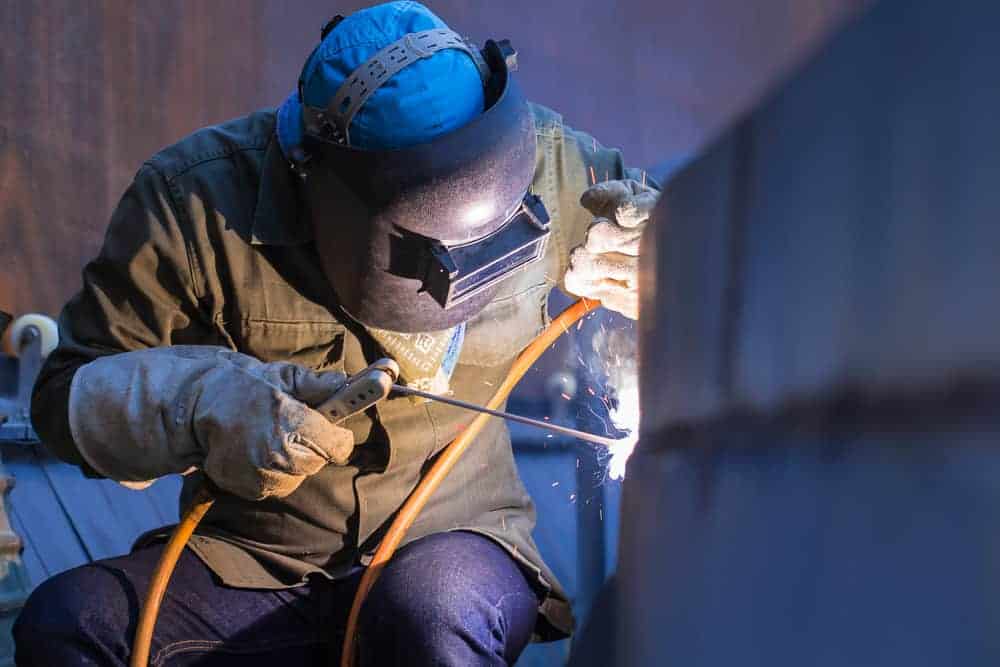
Challenges in Welding Assessment
What obstacles do welding assessors face in their essential function? The intricacies of modern welding methods and products present significant difficulties for examiners entrusted with making certain conformity with safety criteria and structural honesty. One primary barrier is the quick improvement of welding technology; check my site inspectors should continually update their expertise and skills to stay reliable. This recurring education is important to comprehending new materials and procedures, which can differ commonly in characteristics and needs.
Furthermore, inspectors usually come across variations in worksite conditions that can hinder assessment procedures. Factors such as environmental conditions, access, and the physical state of the bonded structures can make complex comprehensive evaluations. Time restrictions imposed by task routines can better push examiners, possibly impacting the thoroughness of their evaluations.
In addition, the subjective nature of some inspection approaches can lead to incongruities in analyses. Aesthetic inspections might vary based on the inspector's experience and viewpoint.
Verdict
Welding inspection is crucial for keeping architectural honesty and safety and security in numerous markets. Through the application of diverse evaluation methods and adherence to established criteria, link inspectors play an essential role in making sure and determining defects compliance with market standards. The challenges encountered in address this field highlight the necessity for continual improvement in examination methods and practices. Eventually, effective welding assessment contributes dramatically to mitigating risks and enhancing the general integrity of bonded structures.
Welding examination is an essential part in the construction and production industries, where the integrity of bonded joints is vital to safety and reliability.Welding evaluation is essential in guaranteeing the integrity and security of bonded frameworks, with studies indicating that up to 70% of architectural failures can be mapped back to poor welding practices. Their responsibilities encompass a thorough range of jobs, consisting of visual assessment of welds, assessing welding paperwork, and performing non-destructive testing (NDT) approaches such as ultrasonic or radiographic testing to recognize issues.
Welding inspectors are likewise liable for translating welding codes and standards, ensuring that the welders are certified and that the products used fulfill the needed demands. Ultimately, reliable welding examination adds considerably to mitigating dangers and improving the overall reliability of welded frameworks.